Follow these steps to ensure you choose the right design partner for your project.
Finding the right partner for your production project can feel daunting. One of the most important parts of this decision is making sure you pick the right partner in design. The design stage of any project is extremely important and acts as the base for your product. Make sure to consider the steps below when choosing your design partner.
Commitment to Your Project
Your design partner’s commitment to your project should be apparent and definite. This means that your designers should be easy to get into contact with, respond quickly to inquiries, take your concerns and opinions into account when completing the design, and complete all necessary preparations and research before beginning the design.

Dedicated Team
A dedicated design team means applying years of experience to every project. This involves both industrial designers and engineers that are consistently in contact with your project team and provide an open and clear channel of communication throughout the design project. One great way to make sure that a design team is dedicated is asking for references, looking at past projects they have completed, asking how they keep in contact with their project teams, and the complexity of past projects they have done. Asking these questions will set your team and your project up for success.

Understanding of your Needs
Being on the same page with your design partner is one of the most critical aspects of creating a product you are proud of. This means that both your team and your design partner share an understanding of the following aspects of your projects:
- Goal Product
- This means sharing the same vision for what your final product will look like, how it will function, and who will use it.
- Testing Results
- Whether you are testing for strength, rigidity, load-bearing limits, or something else; being on the same page with your design partner about what you would like those test results to be and designing a product that will accomplish the results you are looking for is key.
- Functionality
- While this may seem obvious, knowing the end function of the product is an important part of the discussion with your design partner. Knowing what you see as the end-user for your product, how it is expected to function daily, if/how often it will need to travel, the size parameters for this project, etc. are extremely important to discuss upfront with your design team.
- Material Quality
- Knowing what type of material you expect to be included in your project and the quality of that material is critical to the design process. This means discussing the type of material you would like to use, other materials that can be incorporated if needed, the cost of those materials, the reusable nature of the material, the look of the material, and so much more needs to be considered at this early step as well.
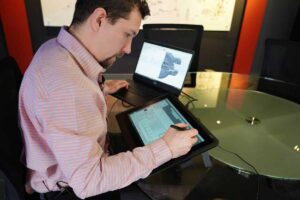
Design and Engineering Capabilities
Lastly, but perhaps the most important part of the process, is knowing your design partner’s capabilities. This doesn’t just mean the design programs they use; it also means understanding how your design partner communicates their designs with the engineering team on the project, what projects they have completed in the past, the scale of projects they have worked on, and their timeline for small and large projects. Evaluating these capabilities from the start helps you to know whether your processes are aligned.
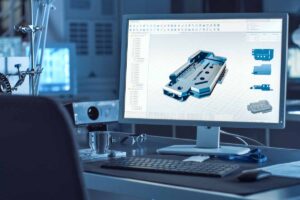
Choosing a design partner can be difficult but when you follow these steps it should make it a little easier. Be sure to keep in mind that your designer should show commitment to your project, have a dedicated team with plenty of experience, have a good understanding of your project needs, and demonstrate exemplary design and engineering capabilities. If you would like to learn more about our Studio 540 design team feel free to read more here and contact us!